A True Cooperative Effort: Revisiting the Farm’s Biomass Project
- Kelley Ellsworth
- May 1, 2024
- 3 min read
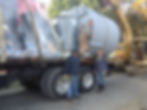
While much of our campus still reads as classic 1800s-1900s New England, our biomass facility houses equipment which appears to be pulled straight from an episode of Ask This Old House. Holding and transfer tanks, circulator pumps, valves, augers, zone controls, and monitoring equipment fill the building—the components of a “district” (aka multi-building) heating system for our lower campus. With installation completed in 2015, a state-of-the-art VETO wood chip boiler replaced an old cordwood boiler—bringing our heating system up from 50% efficiency to ~80-90%, increasing the number of buildings served, reducing emissions to a negligible amount, and eliminating the most labor-intensive pieces of the operation.

Euphemistically known as “Feeding the Beast”, the loading of the old boiler involved splitting ~250 cords a year from our woodlot or donated logs and hand-feeding it into the furnace round-the-clock, every 2-4 hours. One vestige of this process can still be seen out on our fields—a “retired” piece of equipment which gives the impression of an arcade claw toy-grab game, combined with a lifeguard chair and flatbed trailer! Mark Little, maintenance team member and biomass system operator, took me out to show me this swing-arm log loader while recounting what a day-in-the-life used to be like for members of the farm team during the winter. As he wrote in 2014 for the Monterey News,
“Gould Farm proudly states that, ‘We harvest hope,’ but for the farm team it was pretty much just wood all winter. Last season [2013], the distribution system froze up a dozen or so times. Hours were spent in the attic of the dairy barn, with buckets of rags soaking in hot water, propane torches and hoses, with farm team members zipping back and forth to the [former] chicken coop, which seemed to freeze a few times a month. Negative ten degrees on an ATV was a rite of passage. “

The Farm has been fortunate in identifying skilled staff members and outside partners to work on physical plant and facilities projects over the years. Former agricultural director, Wayne Burkhart, and Mark were key personnel involved in the feasibility study, design, installation and maintenance of the new heating system which was acquired through a Dept. of Energy Resources (DOER) and the Massachusetts Clean Energy Center pilot grant program.
“In true Gould Farm fashion, after receiving a number of bids, we ended up doing project management in house." Our whole work program participated alongside engineers, mechanics, and plumbing, HVAC, concrete, and site-work contractors—digging and laying pipe, expanding the facility buildings, and completing the installation. "We have continued relationships with all of the vendors and tradespeople to this day,” noted Mark. [See special mentions below.]

Mark enumerated how guests have also contributed since the system was installed, assisting with building a new hopper (storage) bin to improve the wood chip fuel delivery method, monitoring tasks and recording, installation of an auto-dialer alarm to send out an alert in the event of a system malfunction, and suiting up in PPE to clean the boiler’s fire tubes.
“Based on actual output, all of these teams’ collaborative efforts—staff, guest, volunteer, vendor, and donor—have resulted in the Farm displacing the equivalent of about 5,000 gallons of oil a year! It’s been a real civil engineering and renewable energy journey. And now Gould Farm is harvesting more hope and less wood,” jokes Mark, reprising a turn-of-phrase he once used nearly a decade ago now.